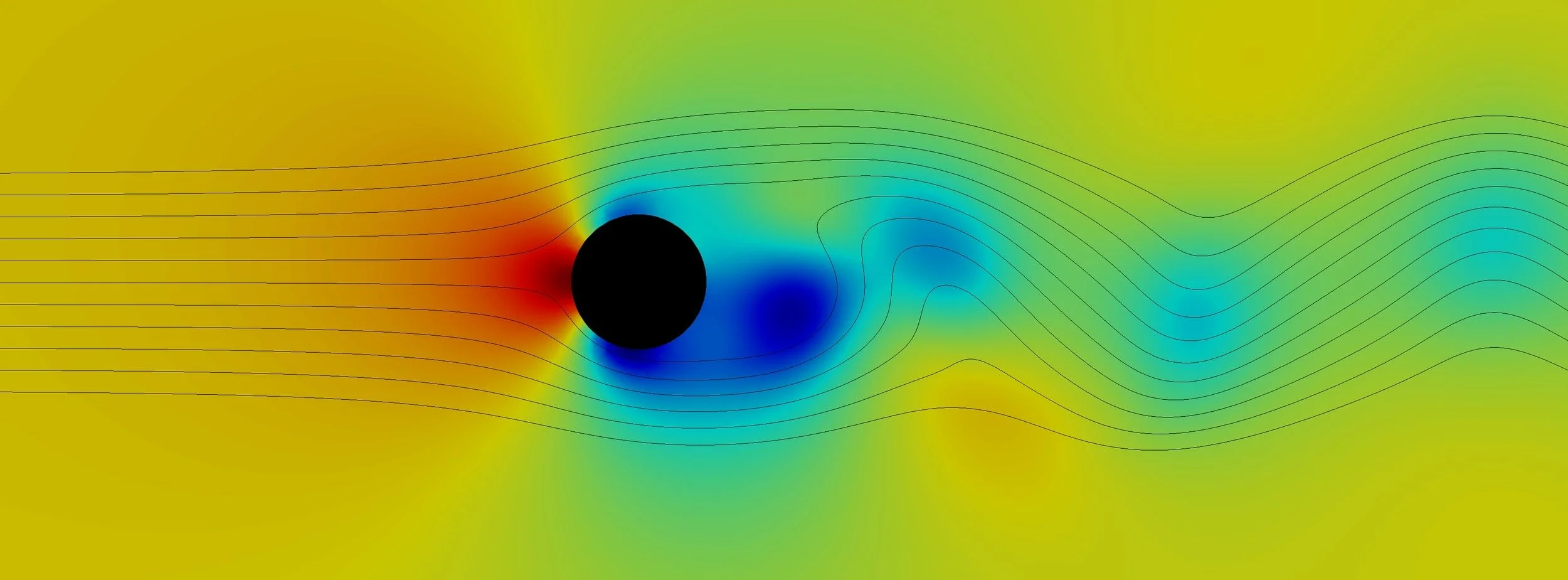
Computational Fluid Dynamics (CFD)
What is computational fluid dynamics?
Computational Fluid Dynamics, also known as computational fluid mechanics or CFD-analysis, is an essential tool for visualizing and analysing the behaviour of liquids and gases. It offers a detailed understanding of flow patterns within the area under study, significantly reducing the need of physical prototypes. By providing information on pressure, velocity, and temperature distributions, flow simulation improves the cost-efficiency of product development and speeds up the development process.
We offer comprehensive CFD analysis for wide range of applications. To read more about our CFD services, visit [our services].
Read about our CFD references by exploring [our references].
CFD applications
Flow simulation and optimization
Flow simulation, analysis, and optimization can be useful in many areas. For example, the airflow inside fireplaces or power plant furnaces can be improved, or the flow in process plants can be balanced and adjusted. By spotting potential flow problems, like high pressure drops, during the planning stage, simulation helps reduce startup risks and lower costs related to pumping and energy losses.
Example applications:
Fireplaces
Electrostatic Precipitators
Manifolds
Air Curtains
Ventilation Systems
Process Optimization:
Cooling Liquid Circulation in Breweries
Biomass Drying
Flow simulation of manifold
Flow field of air curtain
Optimization of rotating equipment and multiphase flows
Pumps and fans are ideal for flow simulations due to the difficulty of measuring details inside their structures. Simulations help improving of pumping and mixing processes by revealing inefficiencies that can be addressed. This approach works for both single-phase and multiphase processes, where simulations can be used to estimate the power consumption of the rotor and to study the effect of geometry modification on flow patterns and pressure losses.
Examples of implementation:
Rotating Equipment
Pumps
Fans
Compressors
Multiphase flows
Ejectors
Water traps
Separators and Filters
Two-phase (water-air) flow simulation of water flow from bottle. See example video here .
Puhaltimen virtauslaskenta
Heat transfer simulations
Heat transfer is crucial in applications involving significant heat generation or temperature-sensitive components, as insufficient temperature control can adversely affect performance. Heat transfer simulations, also referred to as thermal calculations, assist designers in optimizing thermal management of products and processes. Effective optimization enables the use of higher-power components and ensures reliable operation in demanding environments without the risk of overheating. Furthermore, optimizing thermal management enhances efficiency while concurrently it can reduce weight, size, and costs.
Examples of implementation:
Fireplaces
Heat exchangers
Heat pumps
Power plants
Thermal behaviour of tube bundle
Temperature distribution of cold plate
Interested, or is there something you would like to ask?
Petri Hannuksela
CEO
petri.hannuksela( at )foamlab.fi
+358 503815388
Pispalan valtatie 124, 33270, Tampere
"If you would like to discuss the modeling of flows and heat transfer or the possibilities of calculations in general, please feel free to contact us."